
Thermoplastic Adhesive Films for Ballistic Protection (PB)
For optimal conversion of energy introduced by projectiles or fragments, exceptionally high performance is required for ballistic protection systems. Crucial factors are controlled deformation, delamination, or destruction. Beyond that, high adhesion, strength, or elasticity are decisive parameters in the development of ballistic protection products. Choosing the right adhesive system to joining different materials and components is crucial for the overall performance of ballistic protection
Materials for ballistic protection
Advanced ballistic protection systems use and combine high performance materials such as:
- UHMW polyethylene
- Para-aramid
- Carbon fiber reinforced plastics
- Ceramics
- Ballistic steel and other metals
- Glass
- Various other materials
Their combination with different manufacturing processes requires specialized adhesive systems.
Pontacol Adhesive Films for Ballistic Protection
- Pontacol BP monolayer thermoplastic adhesive films
- Pontacol BP multilayer thermoplastic adhesive films
Benefits of Pontacol BP Adhesive Films
- Easy processing of the adhesive
- Defined and consistent adhesive mass distribution
- Broad spectrum of bondable materials
- Combination of different adhesive properties with multilayer films
- Multilayer films allow surface modification to bond difficult substrates or make is accessible for diverse coating and paining processes.

BP Vest inserts
Base set up of a hard ballistic protection plate
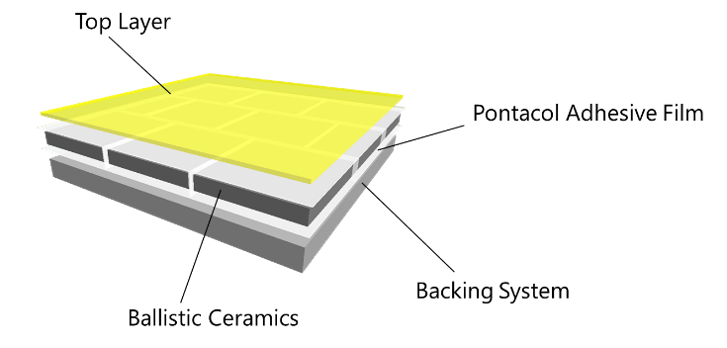
Application Areas of Pontacol BP Films
- Structural components for land, marine and aircraft systems
- Vehicle armor composites
- Spall liner
- Ballistic shields
- Vests and vest inserts
Pontacol BP Films best suitable to bond:
Product | Bonding Temp. °C |
Ceramics | Aramid | PE/UHMWPE | Metals | Glass | Epoxi Resin |
BP21.2007 | 90-130 | + | + | + | + | + | + |
BP21.2008 | 130-140 | ++ | ++ | + | + | + | + |
BP22.2031 | 130-140 | ++ | ++ | + | + | + | + |
BP21.2018 | 100-120 | ++ | ++ | -/+* | -/o** | + | + |
BP21.2019 | 135-150 | + | + | -/o* | -/o** | + | + |
BP21.2053 | 135-150 | + | + | -/o* | -/o** | + | + |
BP20.2017 | 140-150 | + | + | + | + | + | + |
BP22.2202 | 125-135 | + | + | + | + | + | + |
* Depending very much on Matrix system of backing material
** Needs to be tested individually due to different surface treatments